Detectando el Problema: Cómo el Análisis de Causa de Falla puede salvar tu empresa
En el mundo industrial, la fiabilidad y durabilidad de los equipos son cruciales para mantener la eficiencia operativa y reducir costos. Sin embargo, las fallas en componentes y materiales pueden ocurrir, causando interrupciones costosas y, en algunos casos, peligrosas. Es aquí donde el análisis de causa de falla se convierte en una herramienta esencial. Este proceso no solo identifica por qué ocurrió una falla, sino que también proporciona información valiosa para prevenir futuras incidencias. A continuación, encontrarás todos las respuestas para comprender este proceso clave en las industrias.
¿Qué es el Análisis de Causa de Falla?
El análisis de causa de falla es una metodología sistemática utilizada para investigar y determinar las razones subyacentes detrás de una falla en un componente o material. Este proceso implica una serie de pasos que incluyen la recopilación de datos, el examen detallado del componente fallido, la identificación de posibles causas y la implementación de medidas correctivas.
¿Cuál es la importancia del Análisis de Causa de Falla?
Reducción de Fallas Inesperadas:
Optimización de Costos:
Mejora de la Seguridad:
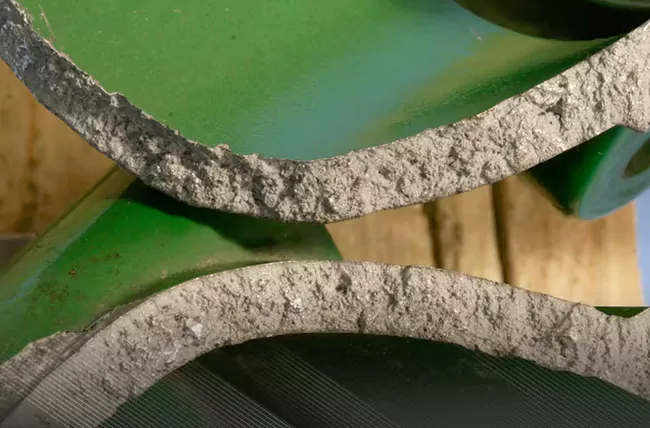
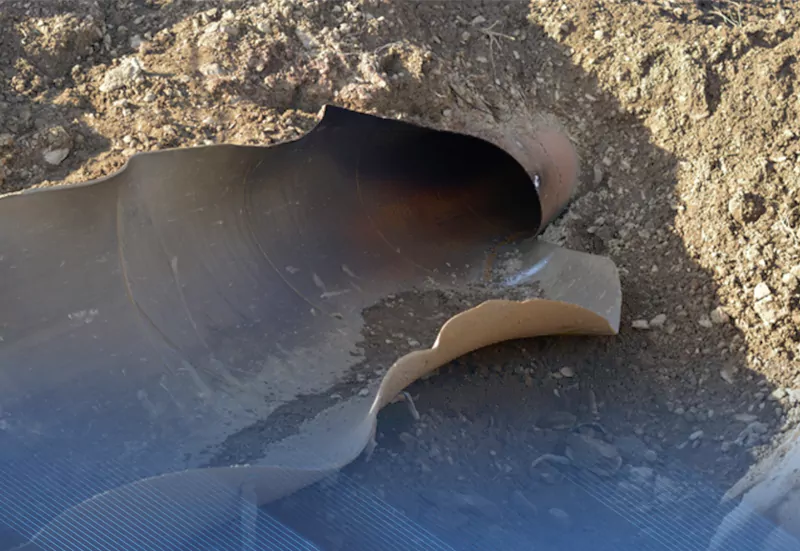
Causas que originan la falla
Es importante detectar el factor que dió origen a la falla, de esta manera se podrá actuar sobre la causa del problema
Para esto, es necesario realizar el proceso con un laboratorio industrial especializado en este tipo de análisis y con procesos certificados.
La competencia resulta clave para este proceso elemental de cualquier industria.
En LABTESA, además de nuestra amplia trayectoria, contamos con los equipos y el personal idóneo para realizar esta tarea tan importante.
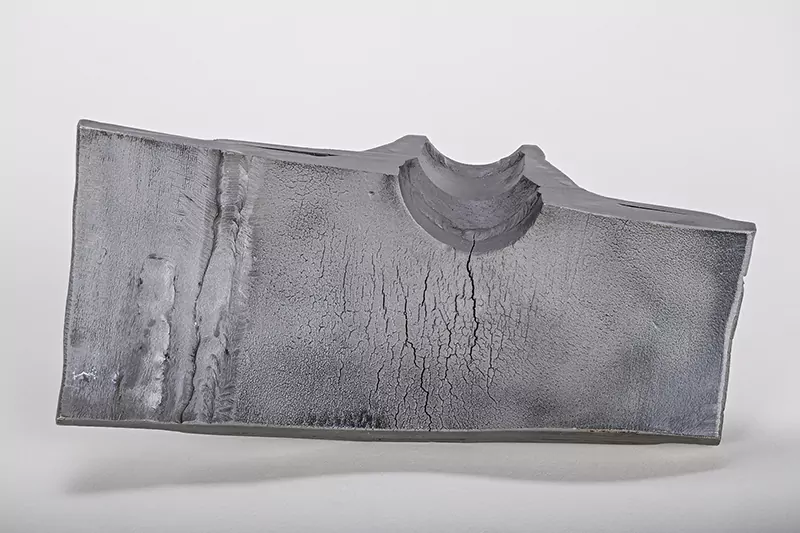
Proceso del Análisis de Causa de Falla
Si bien el proceso resulta complejo, a continuación te contamos los pasos:
Relevar antecedentes:
Reunión con usuarios:
Inspección visual y macroscópica:
Medición de dureza y composición química:
Ensayos no destructivos:
Evaluación metalográfica:
Ensayos mecánicos:
Análisis de dureza Vickers:
Evaluación de resultados:
Conclusiones y recomendaciones:
HERRAMIENTAS PARA REALIZAR EL ANÁLISIS
Para llevar a cabo el análisis de fallas, se pueden utilizar diversas herramientas como el Diagrama de Espina de Pescado, también conocido como Diagrama de Ishikawa. Esta herramienta es fundamental porque permite identificar, organizar y visualizar las posibles causas de un problema de manera estructurada permitiendo a los equipos enfocarse en áreas específicas para la solución de fallas y mejorar procesos de manera efectiva.
El Diagrama de Espina de Pescado recibe su nombre debido a su forma, que se asemeja al esqueleto de un pez. Consiste en un diagrama que parte de una línea central (la "espina dorsal") representando el problema principal. Desde esta línea, se ramifican varias "espinas" menores, cada una representando una categoría de posibles causas, como maquinaria, métodos, materiales, mano de obra, medio ambiente, y mediciones. Dentro de cada categoría, se detallan subcausas específicas.
Casos de clientes
Caso 1:
Falla en el intercambiador de calor de una central termoeléctrica por depósito de residuo interno y sobrecalentamiento localizado.
En una central termoeléctrica, se produjo una fuga repentina de agua en uno de los tubos correspondientes al intercambiador de calor de la caldera. El análisis de causa de falla reveló que esta fuga se originó por la deposición de partículas de cobre y de óxidos de hierro de otro sector de la caldera en el caño, que redujo la conducción térmica de la pared, generando un sobrecalentamiento localizado en esa zona que condujo a la falla.
Como solución, se cambió el tubo afectado, y se realizó una limpieza química en el equipo, para evitar la aparición de este fenómeno en otras zonas.
Caso 2:
En una empresa de energía eléctrica se produjo una falla en conjunto de bulones de componente "v-block" perteneciente a un compensador sincrónico debido a disminución progresiva de la sección resistente por mecanismo de fatiga.
Se debieron descartar otros posibles mecanismos de daño tales como fragilización por hidrógeno, debido a las condiciones de alta exigencia en servicio. El componente funciona con un conjunto de bulones. El debilitamiento y falla por fatiga ocurre en uno de ellos por un desbalance generado en el torque de ajuste inicial, y posteriormente al generarse el colapso, toda la carga es distribuida bruscamente en los bulones restantes que fallan en forma catastrófica y frágil, por elevada velocidad de aplicación de alto nivel de cargas.
CONCLUSIÓN
El análisis de causa de falla es una herramienta poderosa que permite a las industrias no solo entender por qué fallan los componentes y materiales, sino también tomar medidas proactivas para prevenir futuras fallas. Implementar el ACF de manera efectiva puede salvar tus equipos, reducir costos, mejorar la seguridad y aumentar la eficiencia operativa. Al invertir en esta metodología, las empresas pueden asegurar la longevidad y fiabilidad de sus equipos, manteniendo su competitividad en el mercado.